SHOT-BLASTING
Shot blasting is intended to bring to light, by the projection of a metal shot or a mineral abrasive, the substrate of steel, cast iron or aluminum.
This operation is defined by the ISO 8504/2/2000 standard, which classifies the treated substrate in 3 levels of quality: DSa 2, DSa 2,5 or DSa 3, depending on the type of coating subsequently applied and guarantees formulated.
This service is essential for the proper execution of the metallization. It can be effective and used in some cases to carry out stripping work on painted or foundry parts.
Our strong points
- Ergonomics under control, guaranteeing optimum quality
- Handling equipment adapted to heavy loads
- Very short delivery terms
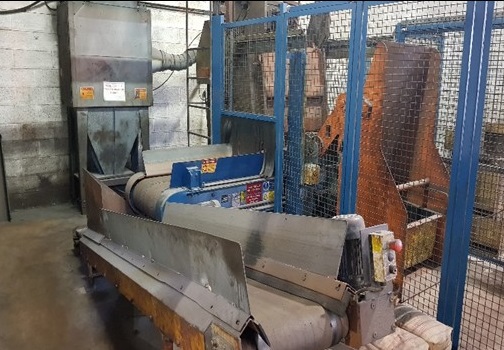
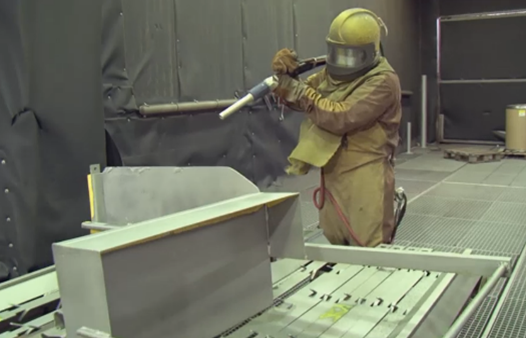
METALLIZATION
Metallization with pure zinc or with zinc-aluminum alloy, provides anti-corrosion protection on all types of steel or cast iron.
Its ease of implementation and the technical performance of this process makes it an economically attractive solution.
It is sometimes used as a substitute for galvanizing, for parts of large dimensions, of complex geometry, or with potential risks of deformation.
During metallization, the zinc, melted by the flame or arc of the spray gun, is fixed on the steel or cast iron, previously stripped by shot blasting Dsa 3 (ISO 8501-1).
This service is defined by standard NF EN 22063 / ISO 2063 and standard NF P 24-351 for the thickness of the coating depending on the exposure medium. The applied thickness of course determines the life of the anti-corrosion coating.
Preparation by shot peening is essential before metallization.
Metalizing, or schooping, should be distinguished from a service often described as powder metalizing, since the latter actually refers to a zinc primer sometimes applied to parts which have not been shot-blasted.
CHOOSE A PLANT